Attention
Only limited support
This entry defines the item entry through which the tool is entered.
At the same time, it is necessary to define a tool store in the options into which the tool can be entered for the interim period if the tool is used. The intermediate inventory should be of the type "Locked inventory".
An automatic transfer of the tool is performed for the setup login of an order.
Workflow:
- Create item for this tool.
No batch- and serial management support.
Item must be stock on default warehouse.
Item must have a stock default warehouse.
- The system will transfer the tool from default warehouse to "tool in production" warehouse.
Create this warehouse and define this in the Configuration wizard:
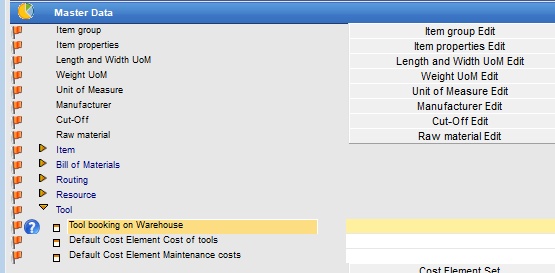
- Insert this tool in routing position.
- Create a work order.
- Log in to this routing position.
The system automatically creates an issue document from Default warehouse.
If no stock is available, the system does not create the issue document. No warning or error message appears.
Then, the system creates a receipt document to the warehouse defined in the Configuration wizard.
- Log out from the routing position.
- You must transfer the tool manually to the default warehouse.
The system does not check if the tool is on stock.
Availability is only visible in the Pool List -> "F2 Open" window.
Limitation:
- System uses standard accounts for manual transactions.
- System uses the price defined in SAP B1.
- System does not support Bin Management.
- System does not check minimum stock or other stock rules.
- No support of work order numbers > 1000000.
|